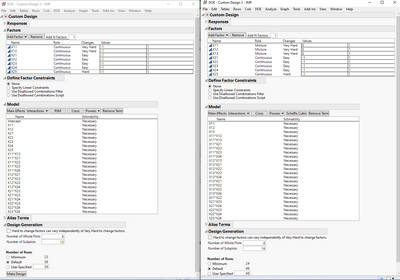
I have a two step process that I am trying to conduct a DOE. The first step is a polymerization process and it has three components adding up to 100%. After the polymerization is completed, the resulted solution will be extruded out to the second step for fiber formation. Because the polymerization step is a batch process and I am not able to vary the composition ratio of the three components until I complete the second step (fiber formation process), I define the factors for polymerization step as very hard to change. There is one hard to change factor and four easy to change factors in the second step (fiber formation). The two steps cannot be separated from each other meaning the solution polymerized from the first step will be extruded out for fiber formation directly from the polymerization reactor.
Since there are three components in the first step for polymerization and they add up to 100%, the first thing coming into my mind is to use a mixture design with X11, X12, X13 as the three mixture factors. However, I am not able to get the main effects for the factors in the second step fiber formation process (X21, X22, X23, X24, and X25). This is the design on the left in the picture. The design on the right of the picture is to define two continuous factors X11 and X12 as the percentage of two out of three components and bound their levels within the interest of study and just make up to 100% with the third component based on X11 and X12. This design can allow for main effect as well as two way interaction for all the factors from the fiber formation process and has higher power than the first design. To me, the non-mixture design is the better one but I am not sure whether I am missing anything or there is a better design than both of the two illustrated here. BTW, for both designs, I am only interested in the main effect for X25, which is a hard to change factor from the second step, to control the reasonable size of experiment runs. Thanks!