Measurement Systems Analysis

Measurement Systems
Measurement systems are used to demonstrate conformity of a product or service to specifications... Without effective measurement systems in place, segregating conforming product becomes more difficult and process controls, process capability and improvement activities may be rendered ineffective.
Measurement systems and associated test equipment need to be suitable for use and capable of producing valid results. Measurement systems can include your data collection methods, work procedures, operators and test equipment.
A measurement systems analysis (MSA) assesses the precision, consistency, and bias of a measurement system. Before you can study the process itself, you need to make sure that you can accurately and precisely measure the process. If most of the variation that you see comes from the measuring process itself, then you are not reliably learning about the process. We use a measurement systems analysis to find out how the measurement system is performing.
Assessing Performance
To determine if a measurement system is accurate and precise and capable of assessing process performance, we need to understand how much variation is due to the measurement system. The gauge repeatability and reproducibility method analyzes how much of the variability is due to operator variation (reproducibility) and how much is due to measurement variation (repeatability).
Any time you measure the results of a process you will see variation. This variation comes from two sources: differences between the parts and the practical limitations in taking the measurements.
Gauge Repeatability and Reproducibility
Total process variation is comprised of part-to-part and measurement system variation. Gauge repeatability and reproducibility studies determine how much of your observed total process variation is due to the measurement system variation and how much is due to part-to-part variation.
Gauge repeatability and reproducibility studies are divided into two components:
- Repeatability is the variation observed when the same operator measures the same part repeatedly with the same device.
- Reproducibility is the variation observed when different operators measure the same parts using the same device.

Industry Guidelines
Industry guidelines recommend that organizations shall conduct measurement system analyses for all new or modified gauges, measurement and test equipment.
i Setting up the study
- Operators measure at least ten parts,
- Select at least three operators for the study,
- Operators should measure each part three times, and
- Select parts that represent the typical process over a significant period.
ii Conducting the study
- Ensure the measurement system has an effective resolution,
- Ensure the operators measure the parts under typical conditions,
- Ensure the operators measure the parts in the same location,
- Ensure operators measure parts in a random order to minimize bias.
iii Assumptions
- The selected parts come from a stable process.
- The measurement device is properly calibrated.
- The operators have been trained in the use of the device
- A specification limit is only required to determine whether the measurement system can be used to accept or reject parts.
Interpreting the variability gauge chart
In this example, we use the Gasket sample data and the Variability Gauge Chart function under the Quality and Process menu. This sample data has five parts measured two times by three operators (note the suggested guidelines). It appears the second part is measured consistently higher than the other parts and the fifth part is measured consistently lower than the other parts. Note that there are differing amounts of variation around the five parts, both within the same operators and between the operators.
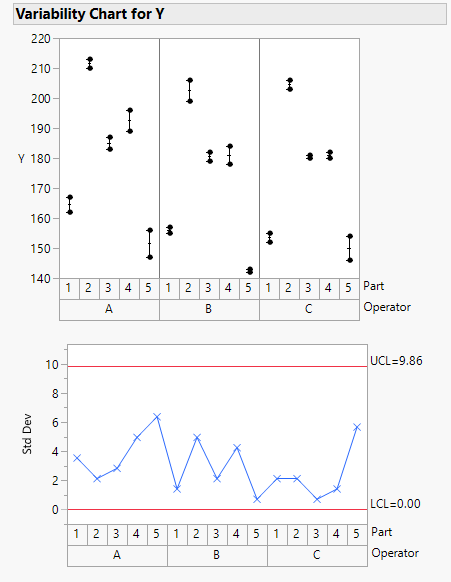
Variability Gauge Chart by Operator
Interpreting the Variance Components for Gauge R&R
The output represents the measurement system variation in terms of its component contribution towards the variance. Recall that variance is the standard deviation squared. Here the variance component for the total gauge is 32.03 and the variance component for part-to-part is 530.81 that sums to a total variation of 562.84. The variance component for the gauge repeatability and reproducibility represents (32.03 / 562.84) *100 = 5.69% of the overall variance.
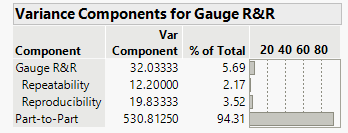
Interpreting the Measurement Source for Gauge R&R
In the next session output, the third column is study variation which equals the standard deviation (square root of the variation) multiplied by a factor of six. For the Gauge Repeatability and Reproducibility component [√(32.03)*6] = 33.96. For the total variance (TV) component [√(562.84)*6] = 142.34. If you have a tolerance, the fourth column displayed is expressed as a percentage of the tolerance.

To adequately assess process performance the measurement system variation is expressed as a percentage of the total variation. To segregate conforming product the measurement system variation is expressed as a percentage of the tolerance. Based on industry guidelines, the acceptable percent measurement system variation is less than 10%. Greater than 30% measurement system variation is not acceptable.

The Gauge Repeatability and Reproducibility (RR) component divided by the total variation (TV) component is equal to (33.96 / 142.34)*100 = 23.85%. Based on the guidelines, this measurement system could do with further improvements.
One more important point to note, the number of distinct categories represents the divisions the measurement system is capable of discriminating within the process. The target is for greater than 5 distinct categories. That is the measurement system should be able to measure and distinguish between five distinct categories that is: very low, low, medium, high and very high measurements. In this case, the number of distinct categories equals to five, so the measurement system can discriminate between very low, low, medium, high and very high measurements.
Learning Resources
To get started, I recommend these useful learning resources.
https://www.jmp.com/en_au/events/getting-started-with-jmp/overview.html
In addition, there is an e-learning course covering statistical thinking for problem solving. This course includes seven modules; one of which is a module on Quality Methods such as Measurement Systems Analysis... Each module comes with a certificate of completion that users can post as a record of achievement.
https://www.jmp.com/en_au/online-statistics-course.html
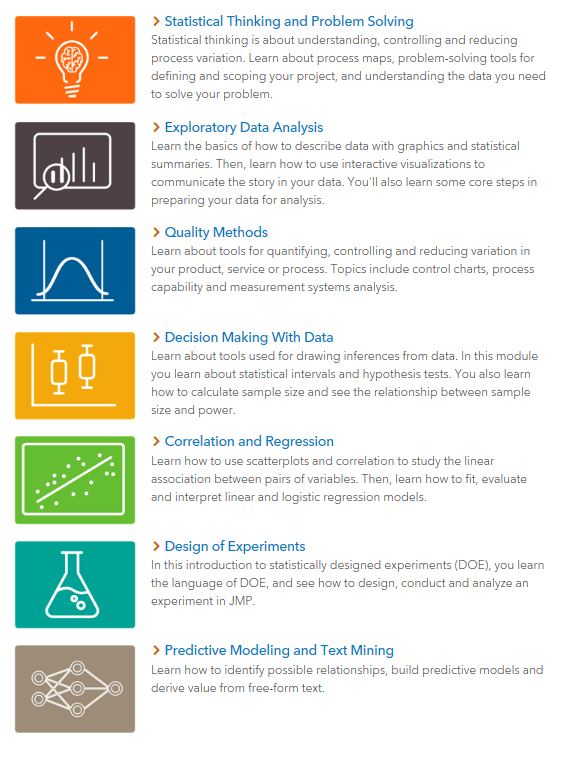
If your team would like to attend a training class on Quality Improvement and Measurement Systems Analysis, please take a look at the JMP Education Online Course Catalogue.
You must be a registered user to add a comment. If you've already registered, sign in. Otherwise, register and sign in.